3D printing is undeniably one of the most spectacular inventions in the realm of additive manufacturing, revolutionizing the concept of making complicated geometries without the need for mold or other mass manufacturing processes. Despite its capacity to produce intricate, bio-inspired, multi-material designs, 3D printing is not yet ready for large-scale manufacturing.
Due to the growing demand for flexible items in a variety of applications, researchers are exploring beyond traditional 3D printing, which fabricates structures from a single material, to construct a meta-material structure. These structures are generated by the force acting at the intersection of two composite materials when subjected to external stimuli.
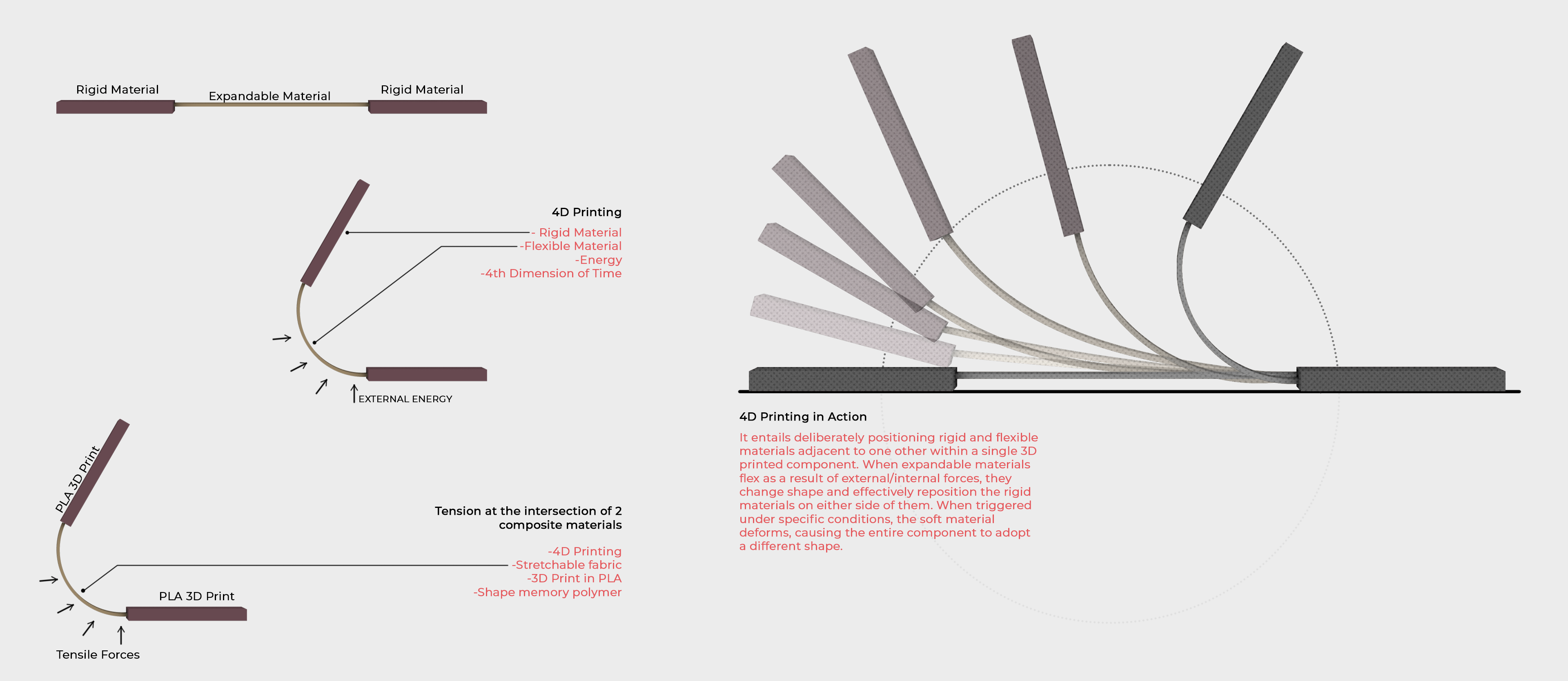
The research is a reflection of an architecture student attempting to capture the spontaneity and emergent behavior of materials and fabrication techniques. Architecture and material are inextricably linked. Deformation Tectonics is a study of a specific type of material tectonics and its related design strategies. Trying to understand the capabilities of 4D printing for architectural systems.
WHAT IS 4D PRINTING?
The addition of the fourth dimension to 3D printing technology is known as "4D Printing." With this new dimension, 3D printed objects may alter shape independently of environmental stimuli such as light, heat, electricity, magnetic fields, and so on. The capacity of 3D printed things to change shape over time in reaction to specific stimuli is based on the material's ability to morph over time in response to specific stimuli, and it does not require human interaction to facilitate the process.
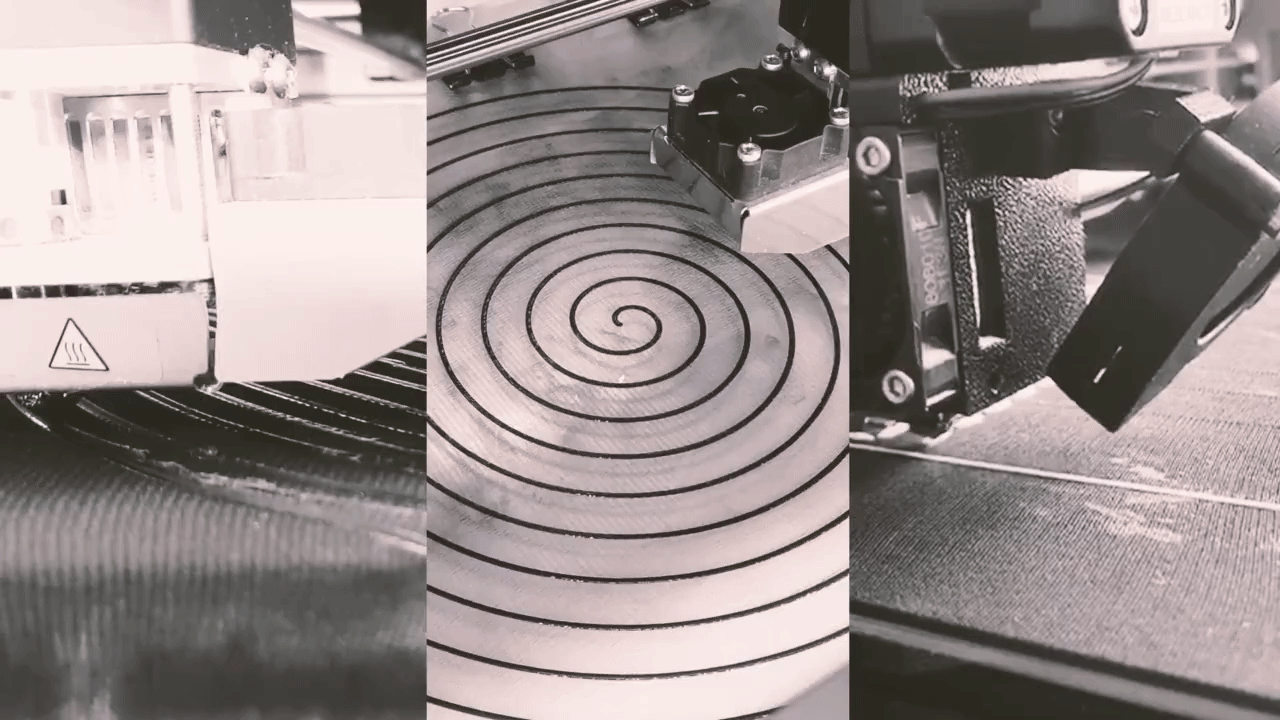
4D Printing Process:
What I'm attempting to do is to expand on Skylar Tibbits' study of 3d printing a single layer of shape memory polymer on pre-stretched fabric, and once the fabric is released, it offers a three-dimensional form with a fourth dimension of time acting on it. Because the material contracts and deforms it becomes forgiving in precision. However, it is still difficult to control. Therefore, some construction strategies need to be developed for additive construction.
Equipment:
For the prototype, I utilized a desktop 3D printer with manual bed modifications, where the elastic fabric is clipped on and PLA is printed layer by layer through the nozzle.
1. Cr10 Desktop 3D Printer
2. Bed size -
3. Print Nozzles:
4. PLA Filament (Shape Memory Material)
5. Stretchable Fabrics (Heat resistant)
2. Bed size -
3. Print Nozzles:
4. PLA Filament (Shape Memory Material)
5. Stretchable Fabrics (Heat resistant)
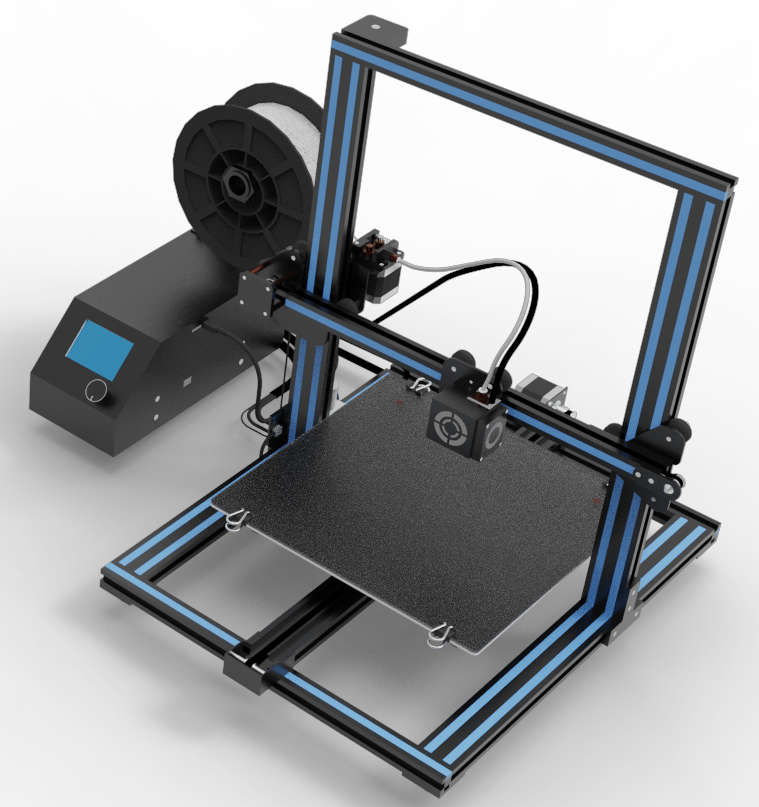
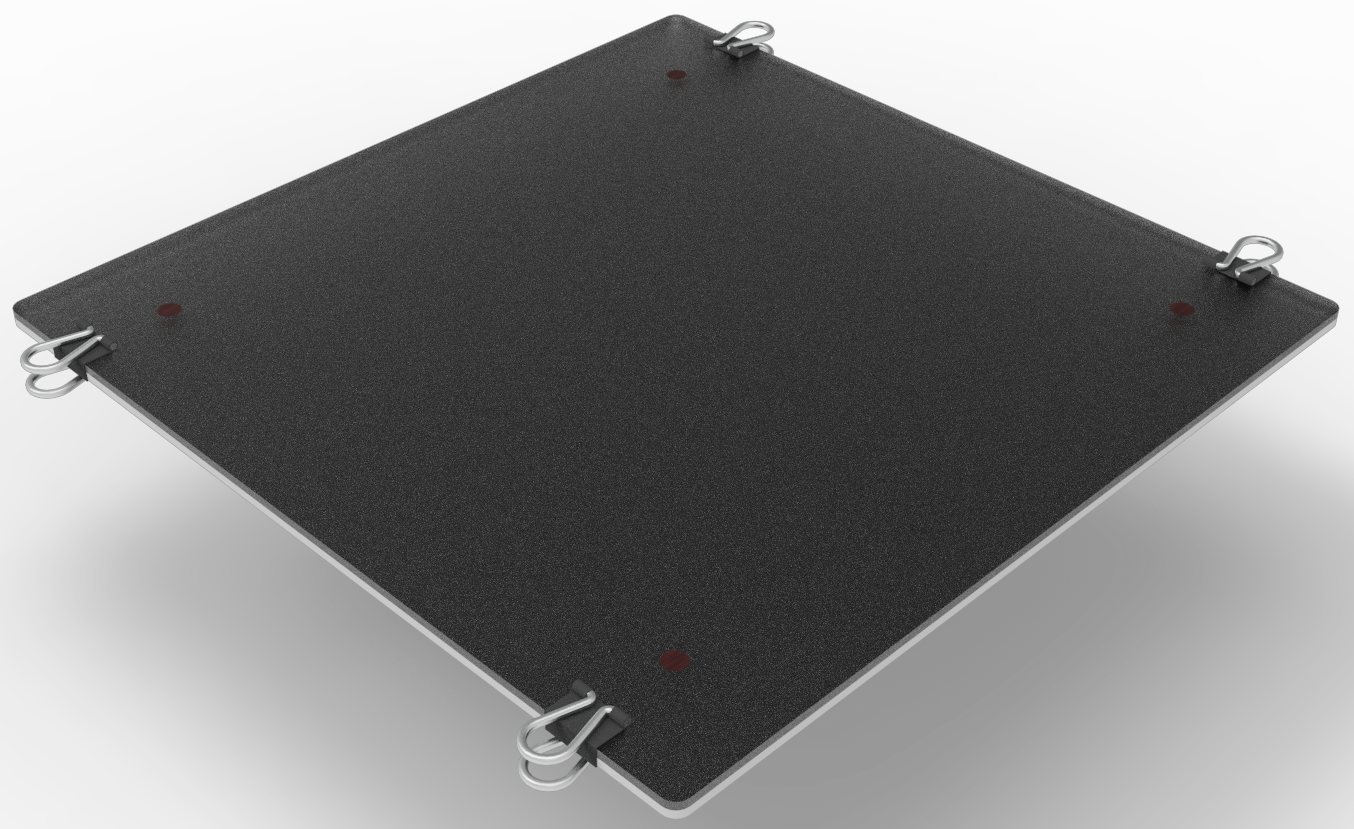
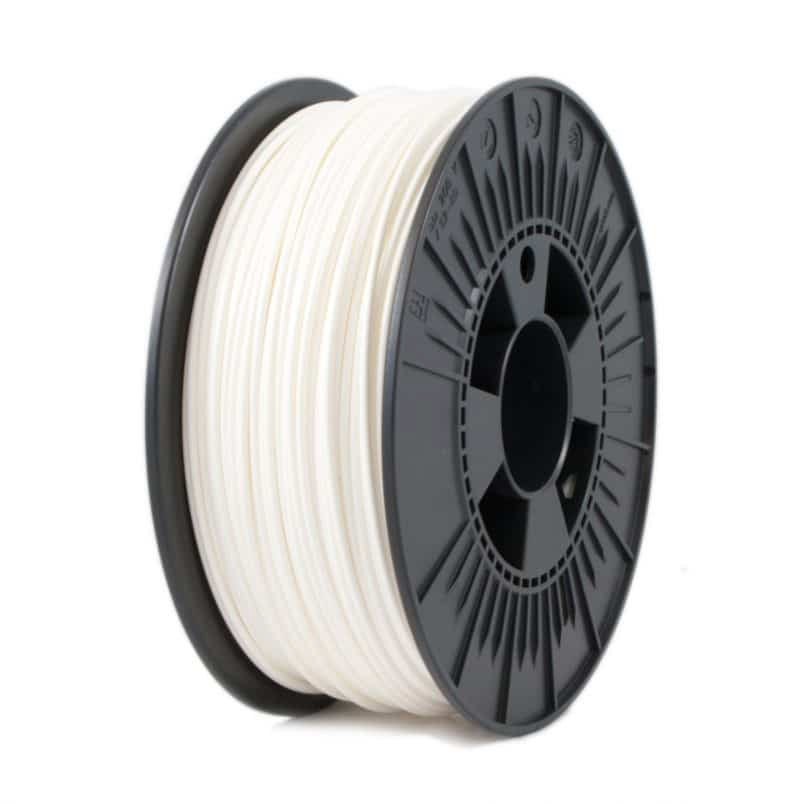
FUNDAMENTALS OF 4D PRINTING
My initial study focused on the deformations that occur when basic 2D Patterns are 3D-printed with shape memory polymers on different stretchy fabrics, investigating fabrics’ heat resistance, stretchability, and interaction with filaments. Basically, physical experimentation.
Experiment 101: Testing Heat Resistance
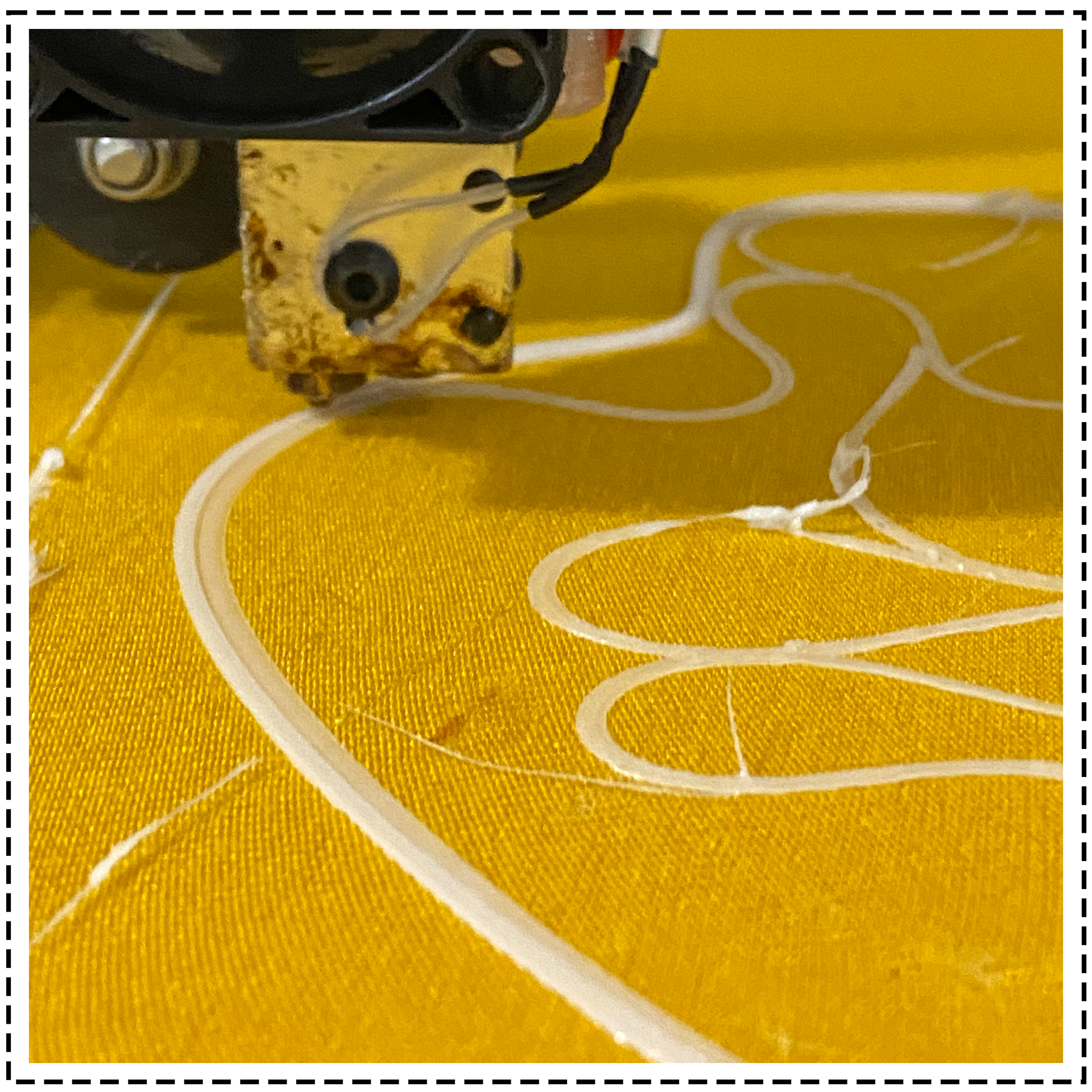
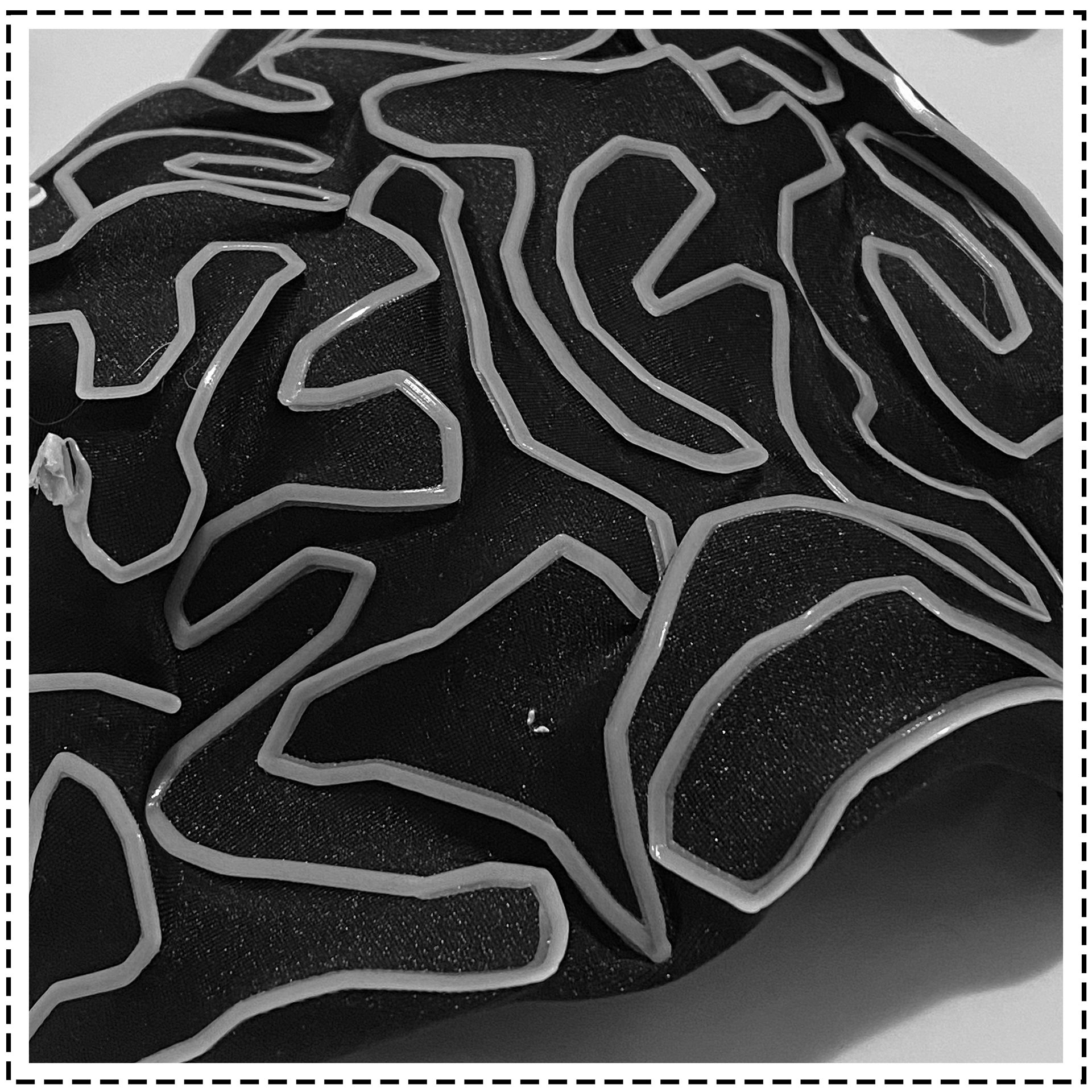
Experiment 102: Testing Stretchability
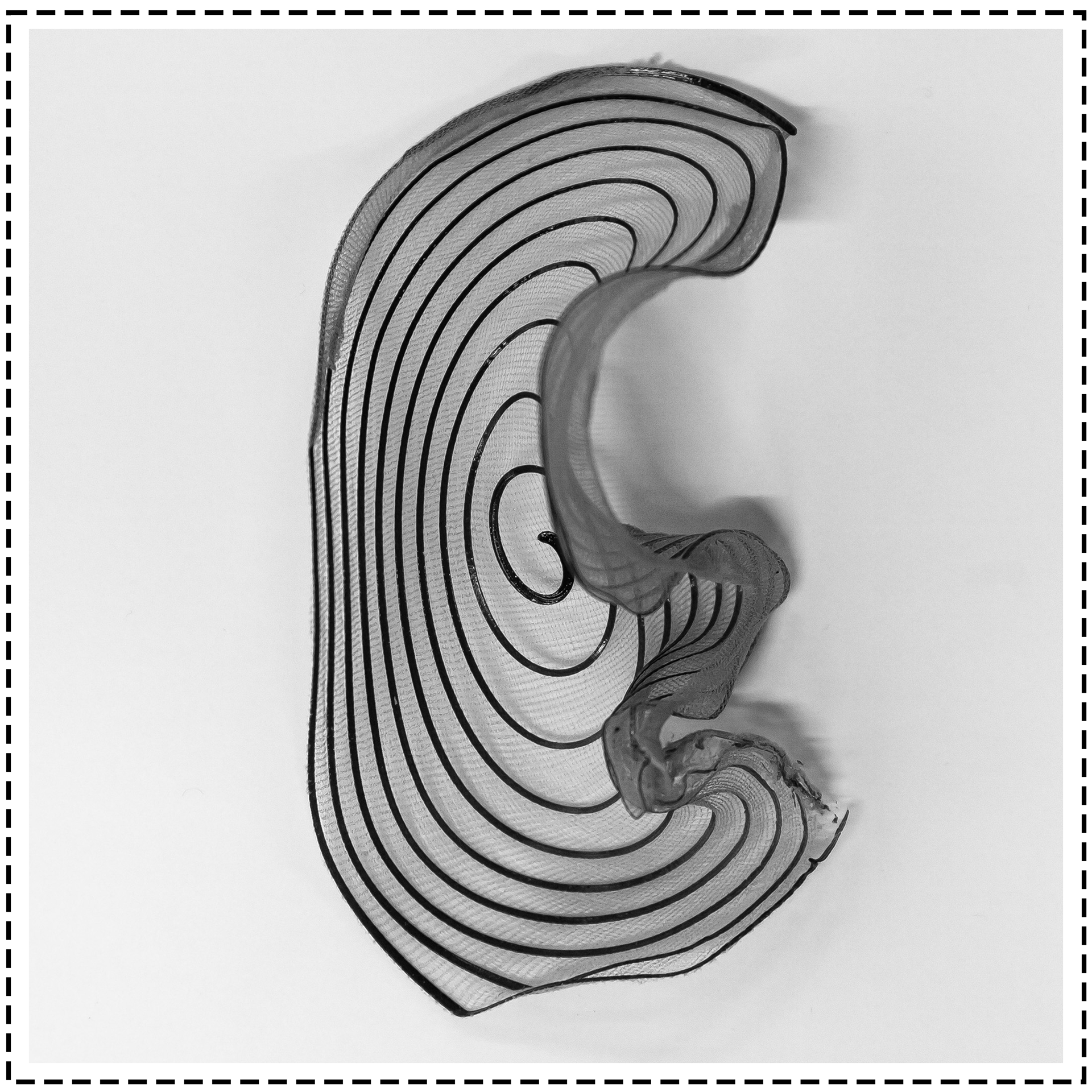
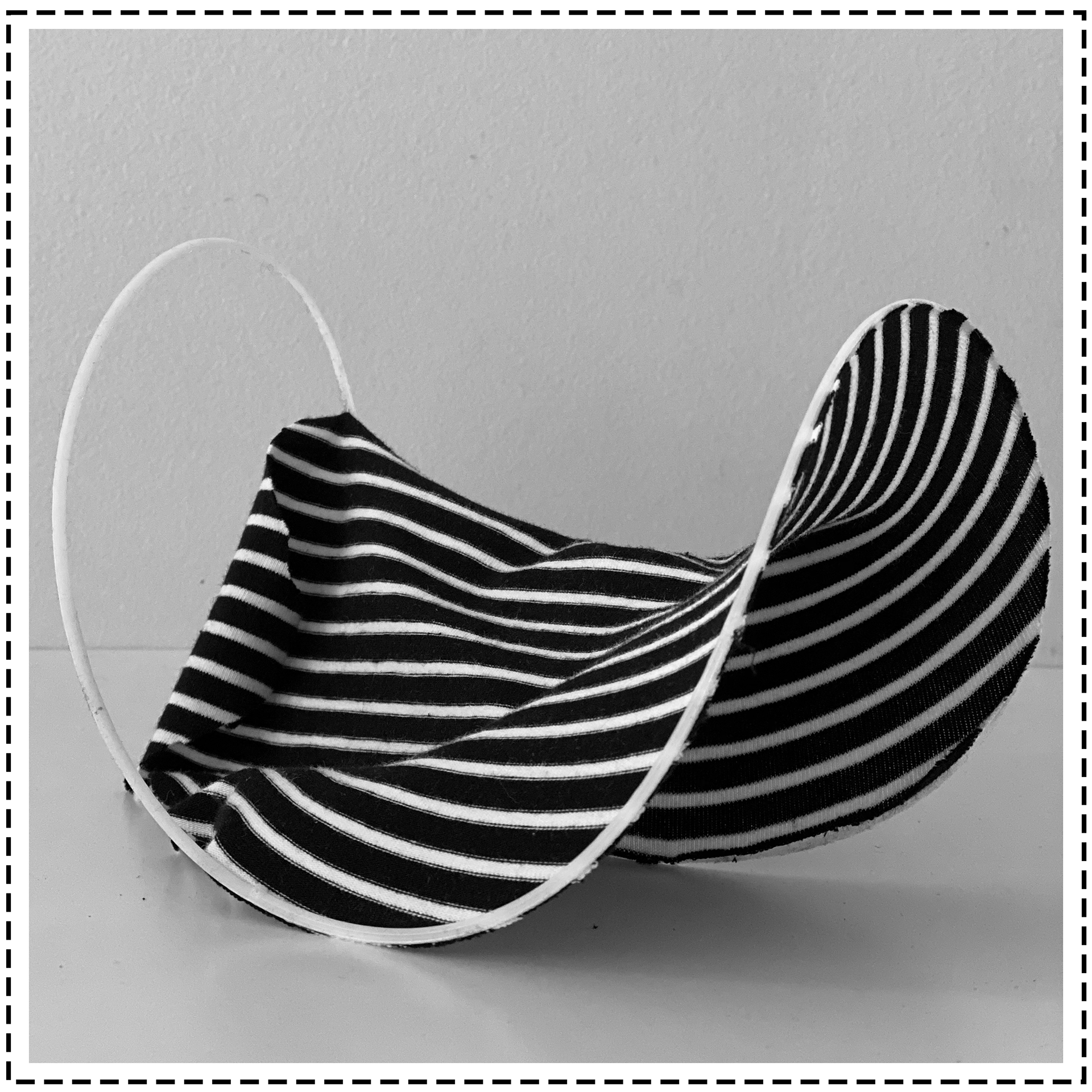
Experiment 103: Testing Nozzle size and layer heights
ANALYSING THE PROTOTYPES
The PLA filament that is primarily used for 3D printing is a thermoplastic substance, which means that it becomes malleable or moldable above a certain temperature and hardens upon cooling. As a result, when the prototypes are heated, the printed pattern becomes less rigid while the forces of fabric stretching predominate and the deformation becomes more dramatic. Except when an external force is applied, when the pattern is cooled in a different location, it stiffens again.
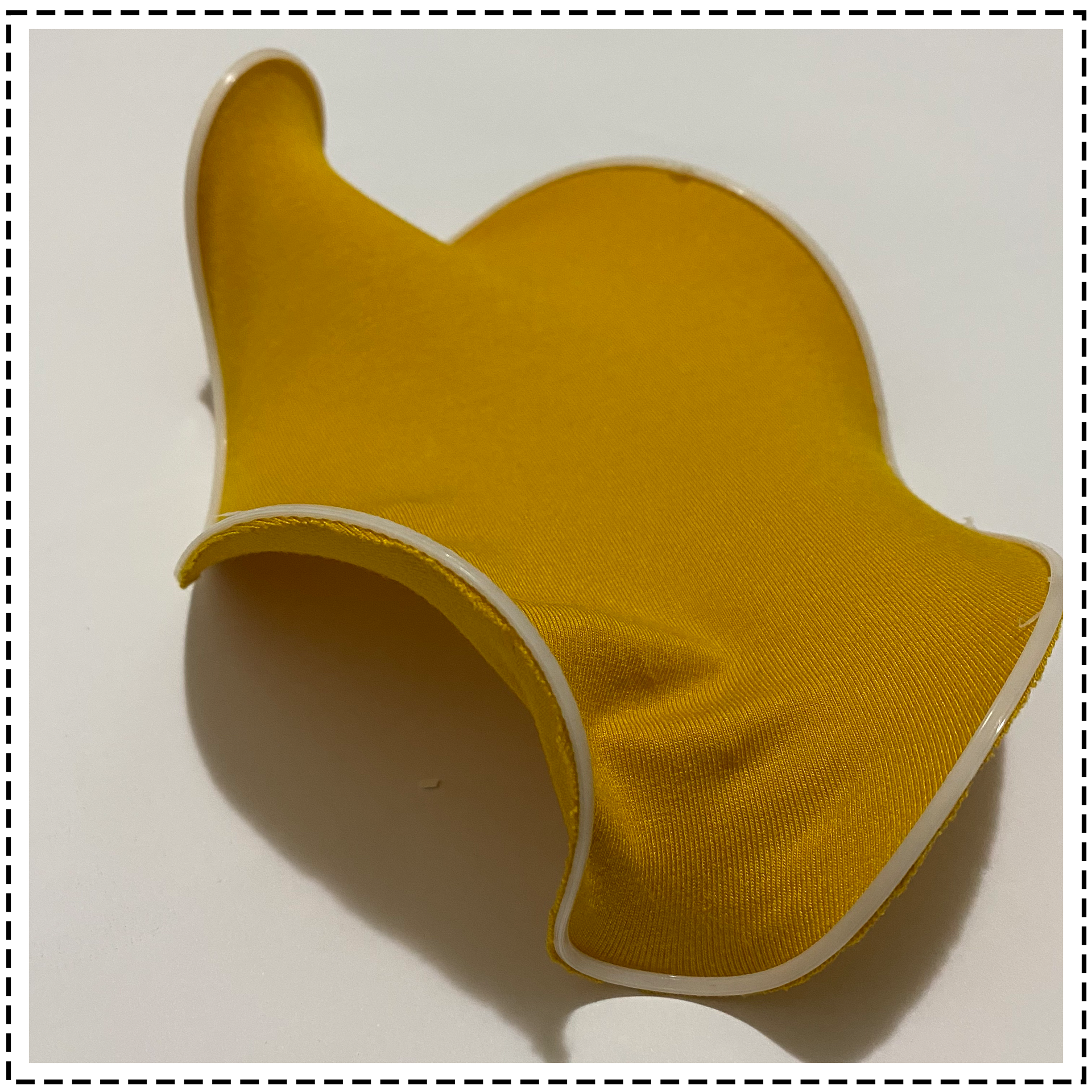
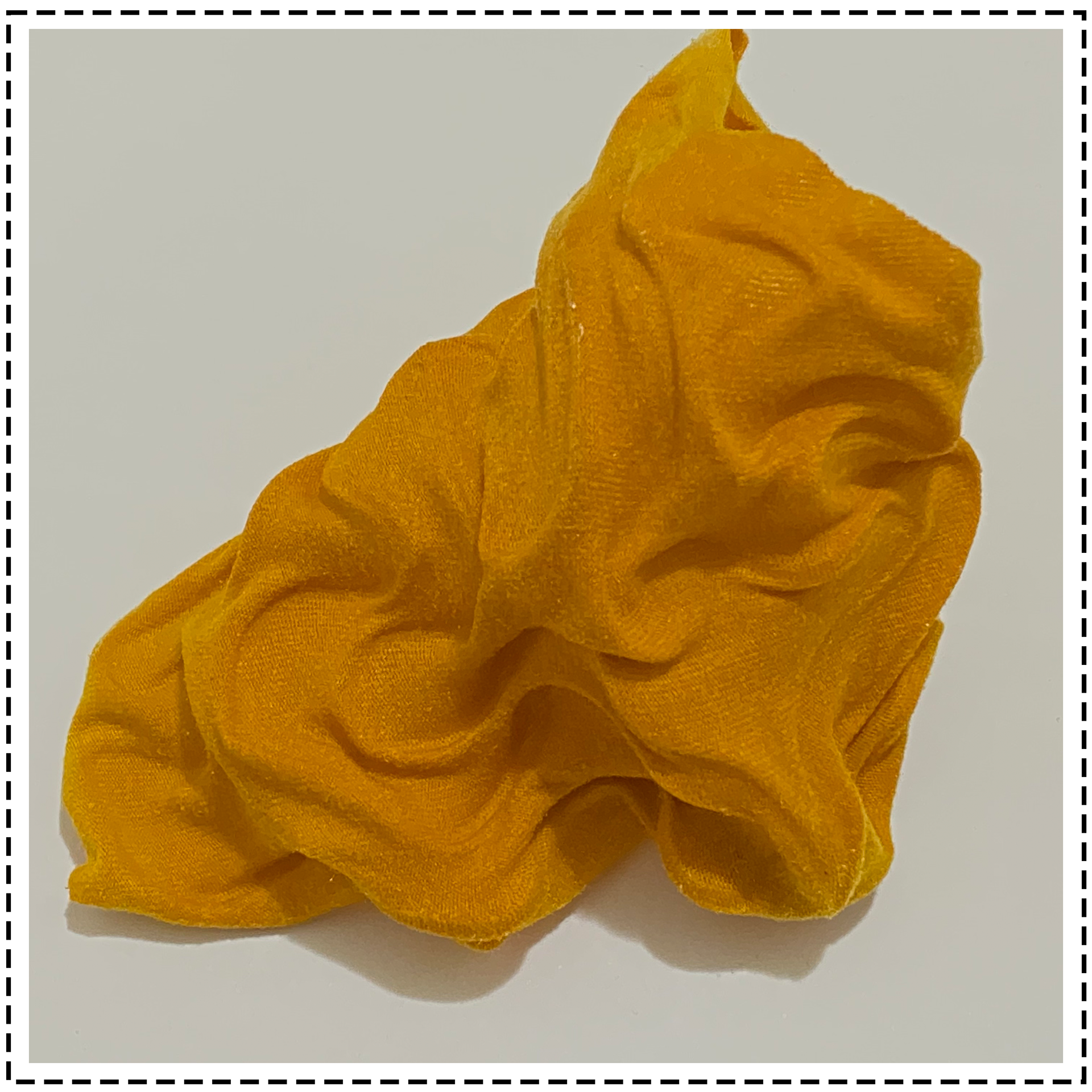
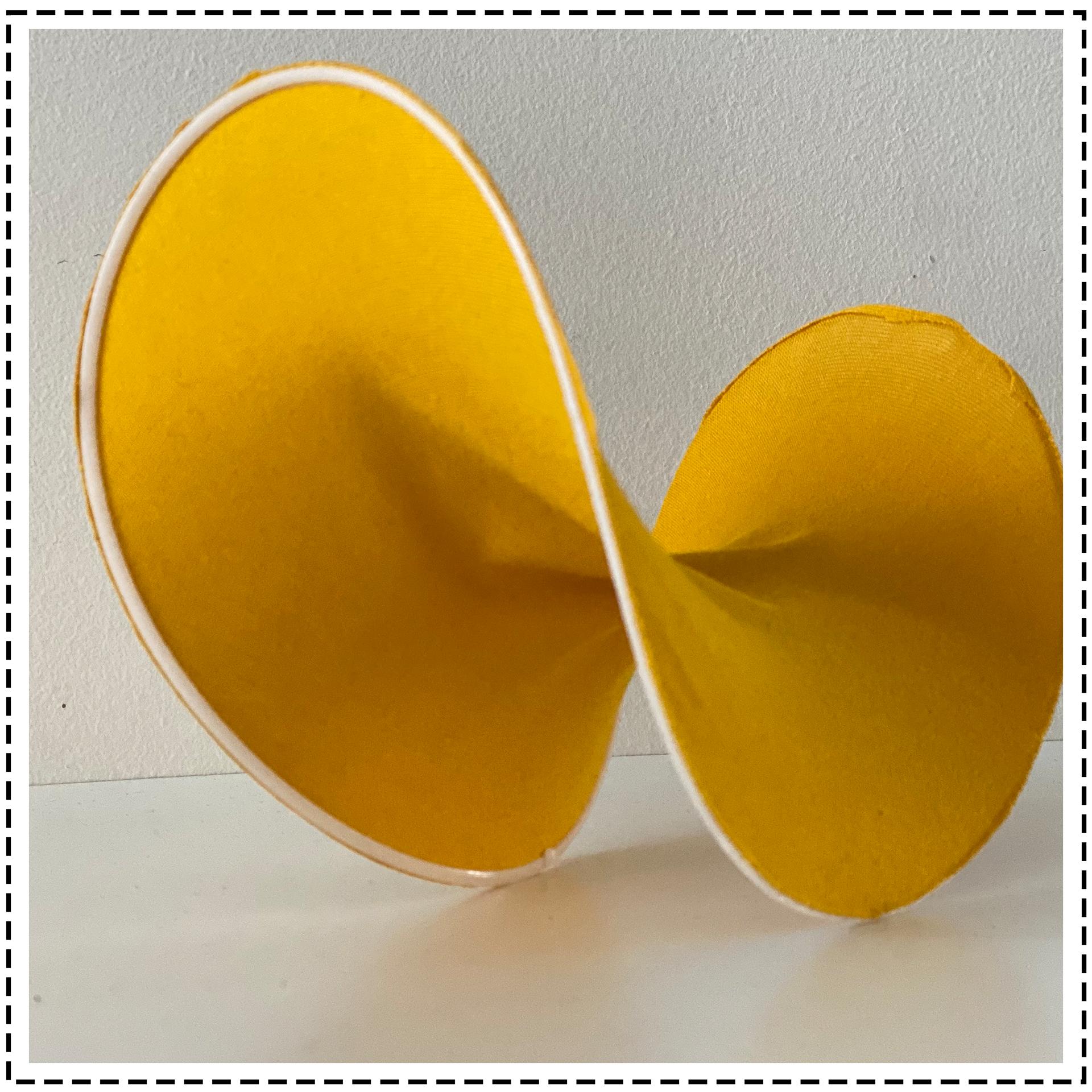
DIGITAL FABRICATION
The gathered findings are utilized to create a digital physics simulation that replicates the real-time deformation and might be utilized for form finding at the architectural scale. This programmable deformation can help with the conceptualization of dynamic formations
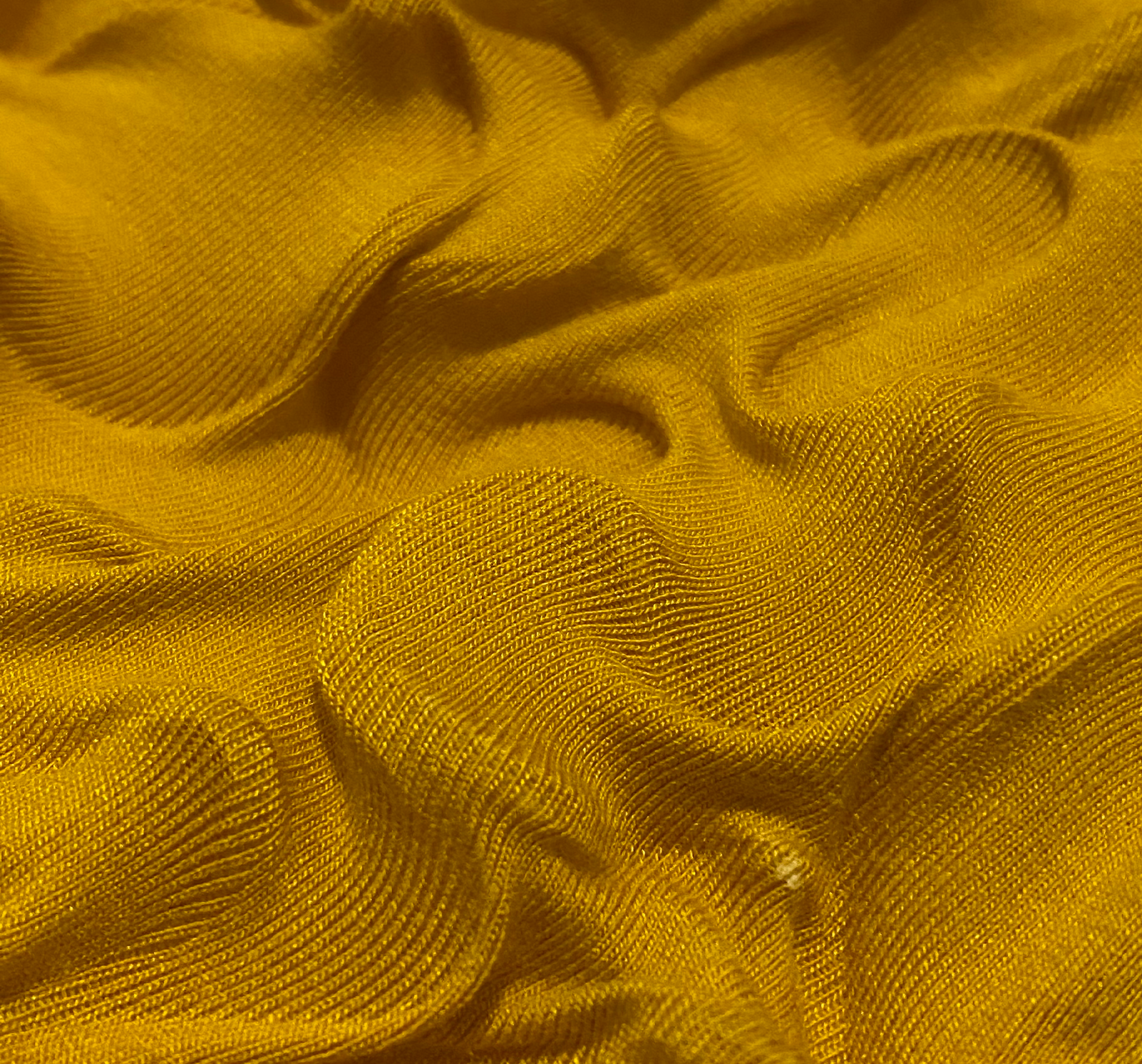
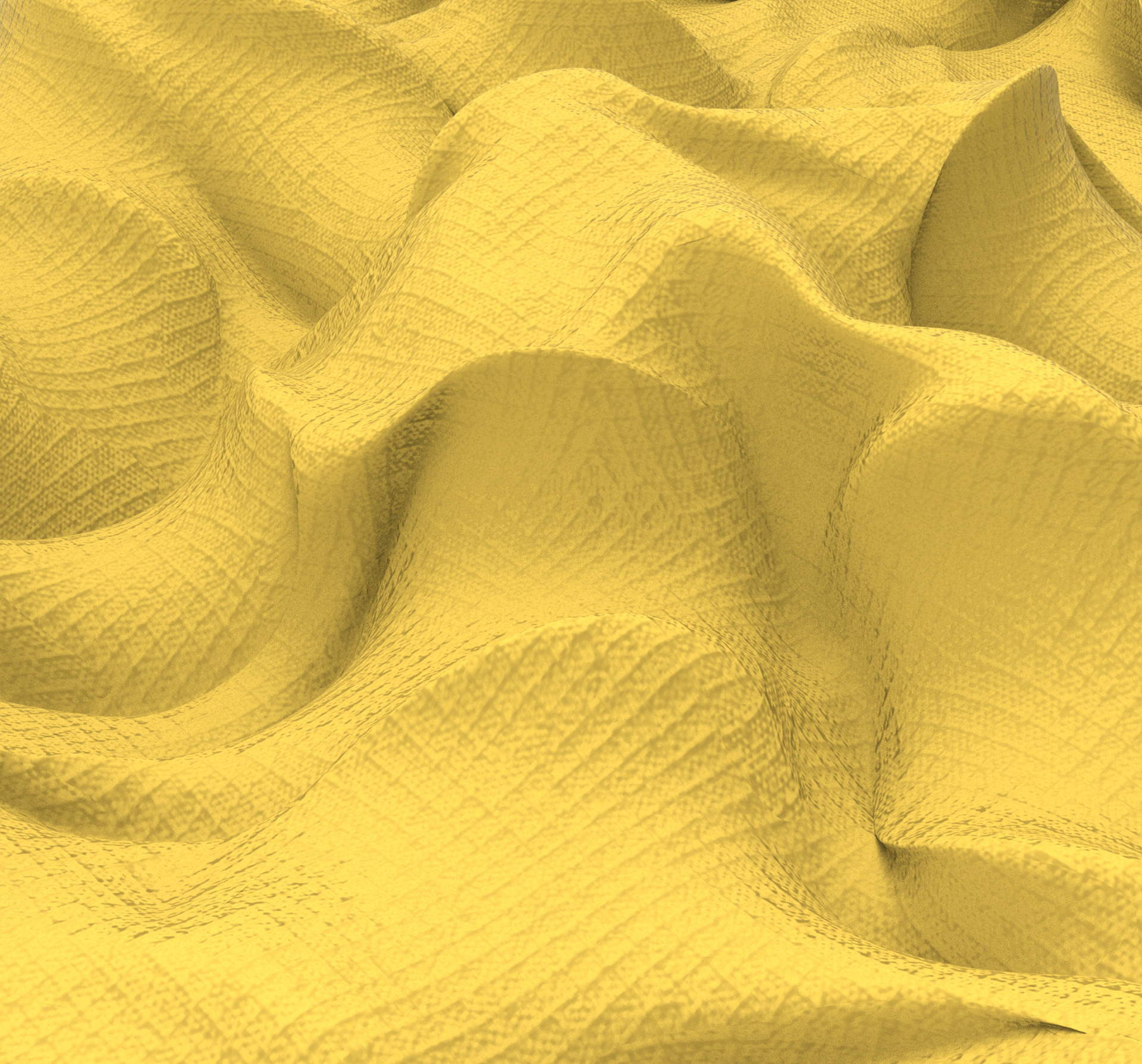
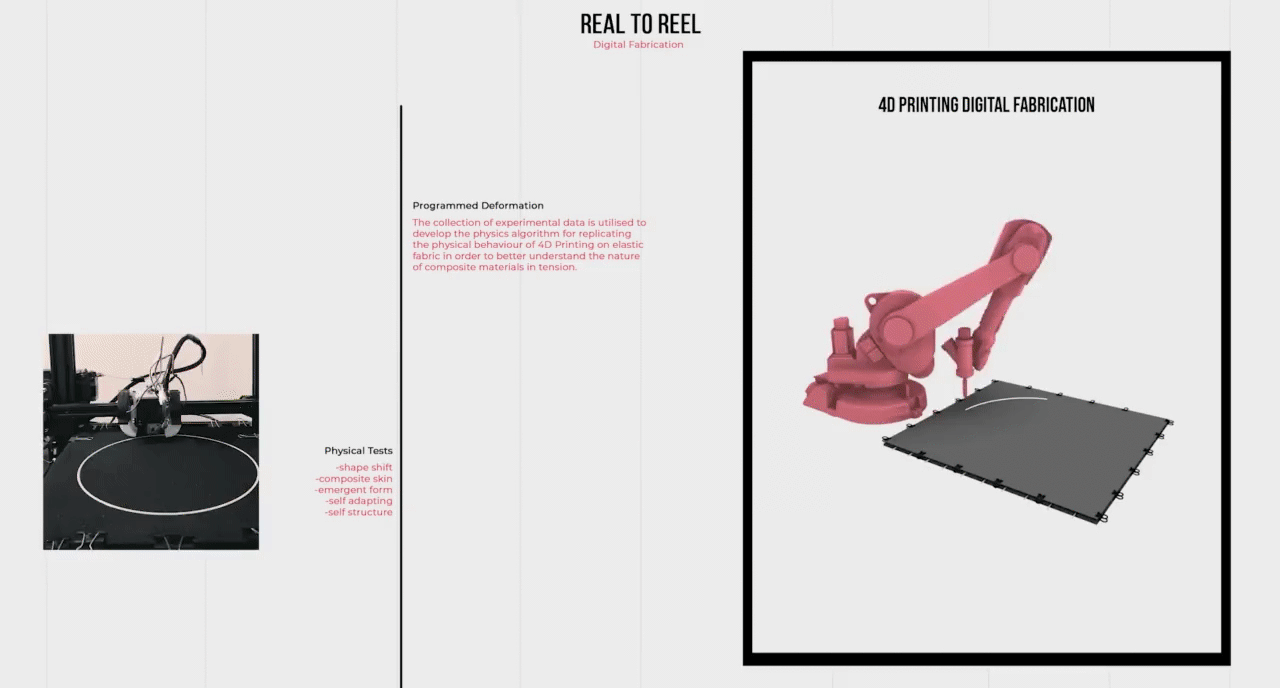
REFLECTION
The result of the research was at the intersection of robotic 4d printing as a negotiation between digital simulations and physical materiality. Where design happens in between emergent form development and attaining ordered structural stability only through the local interaction.
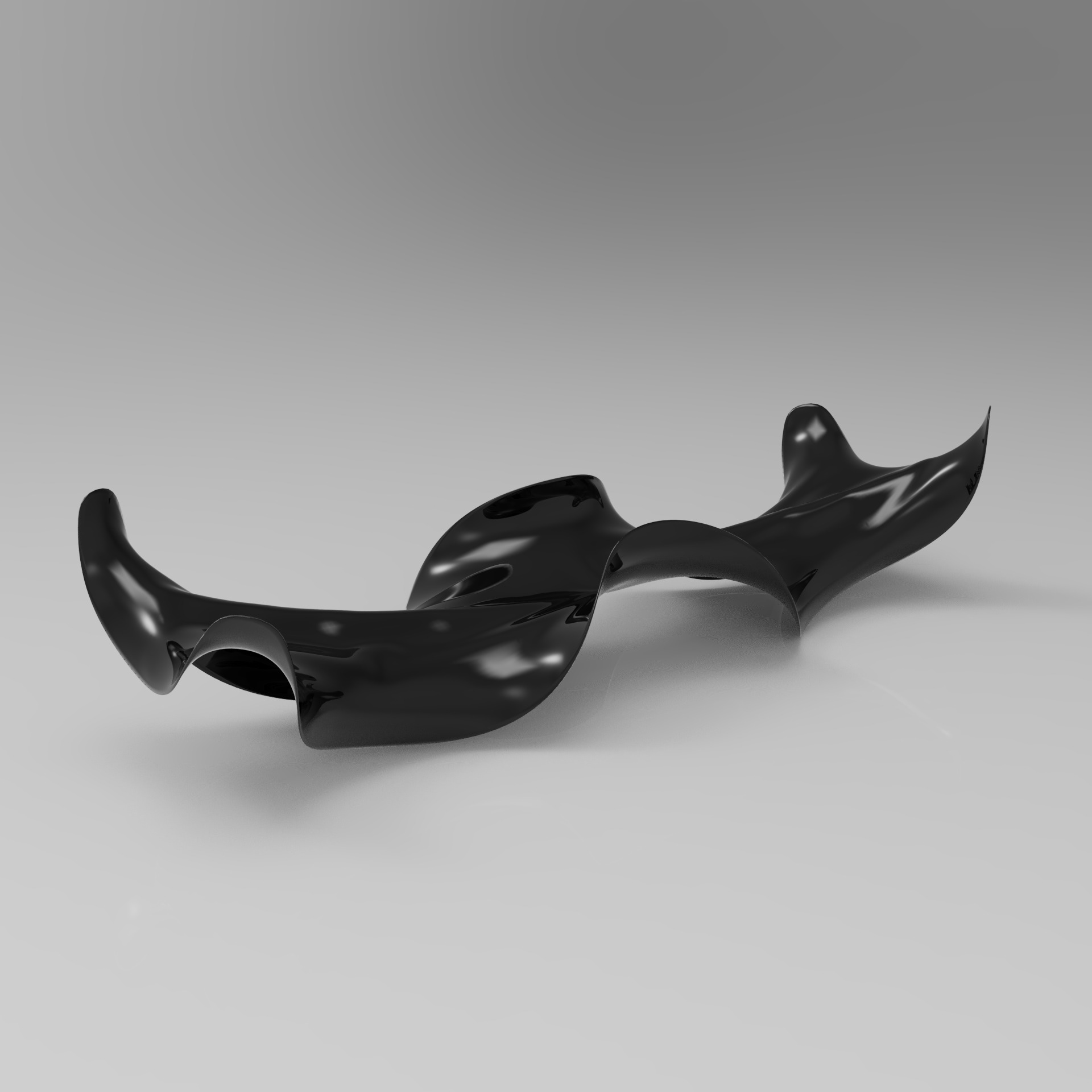
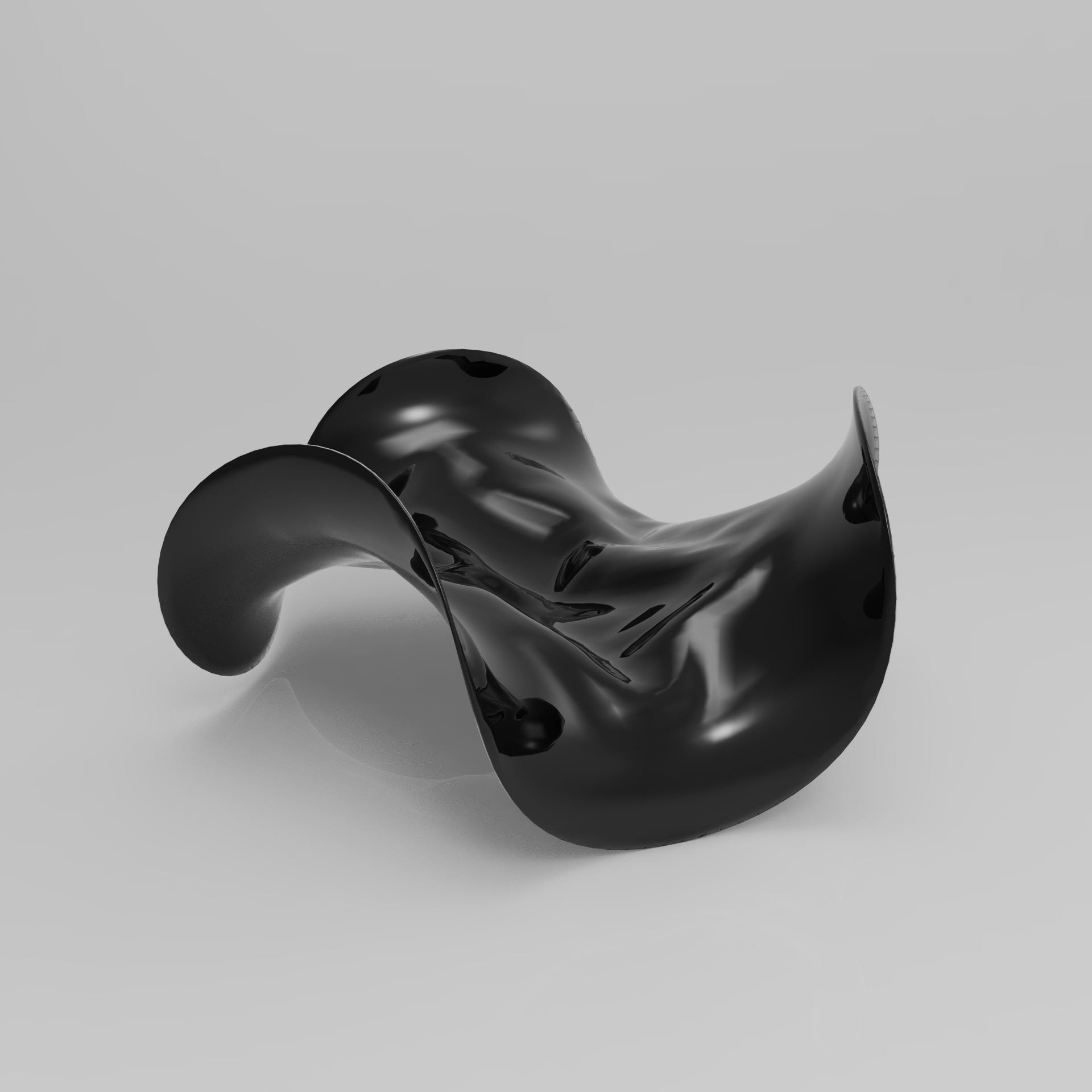
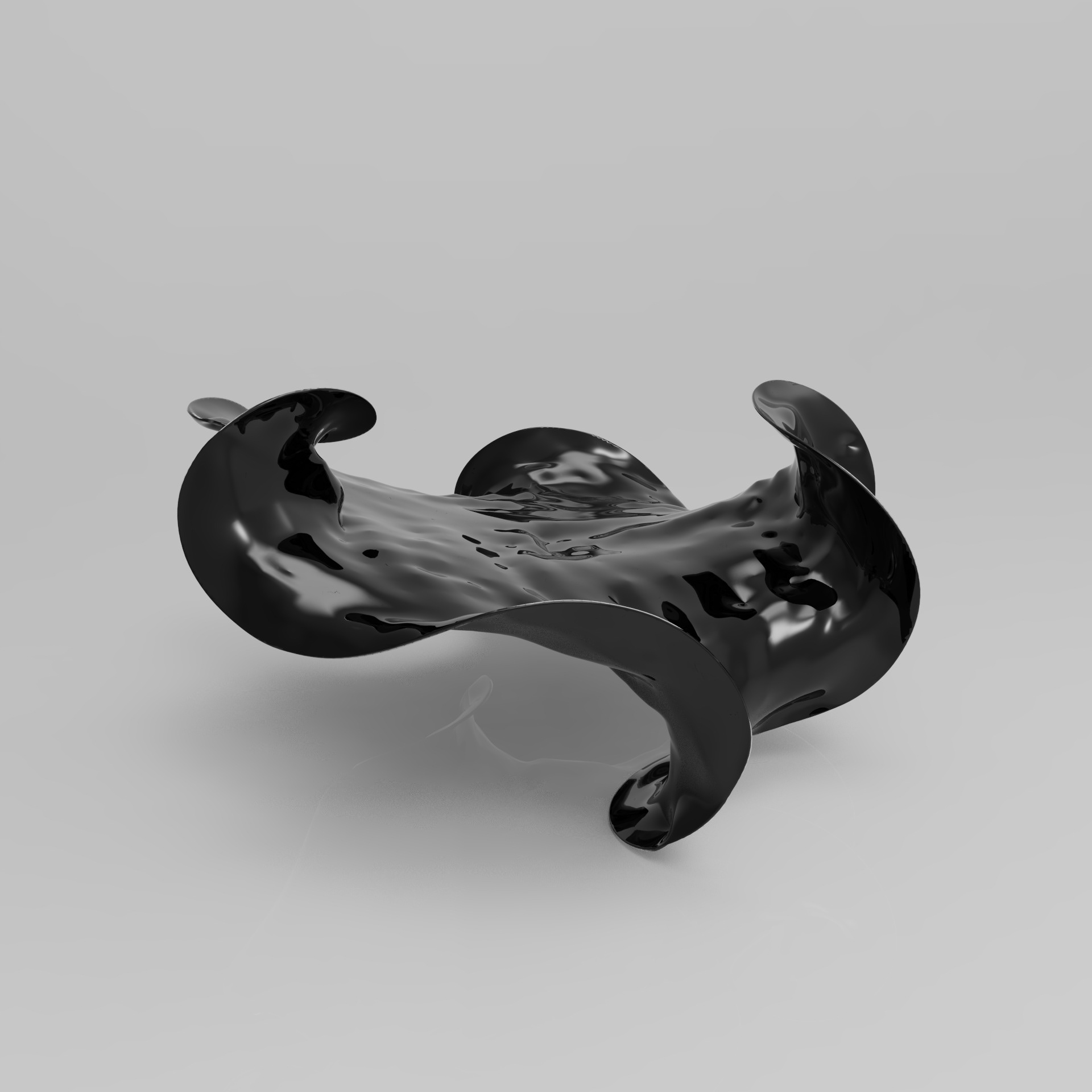
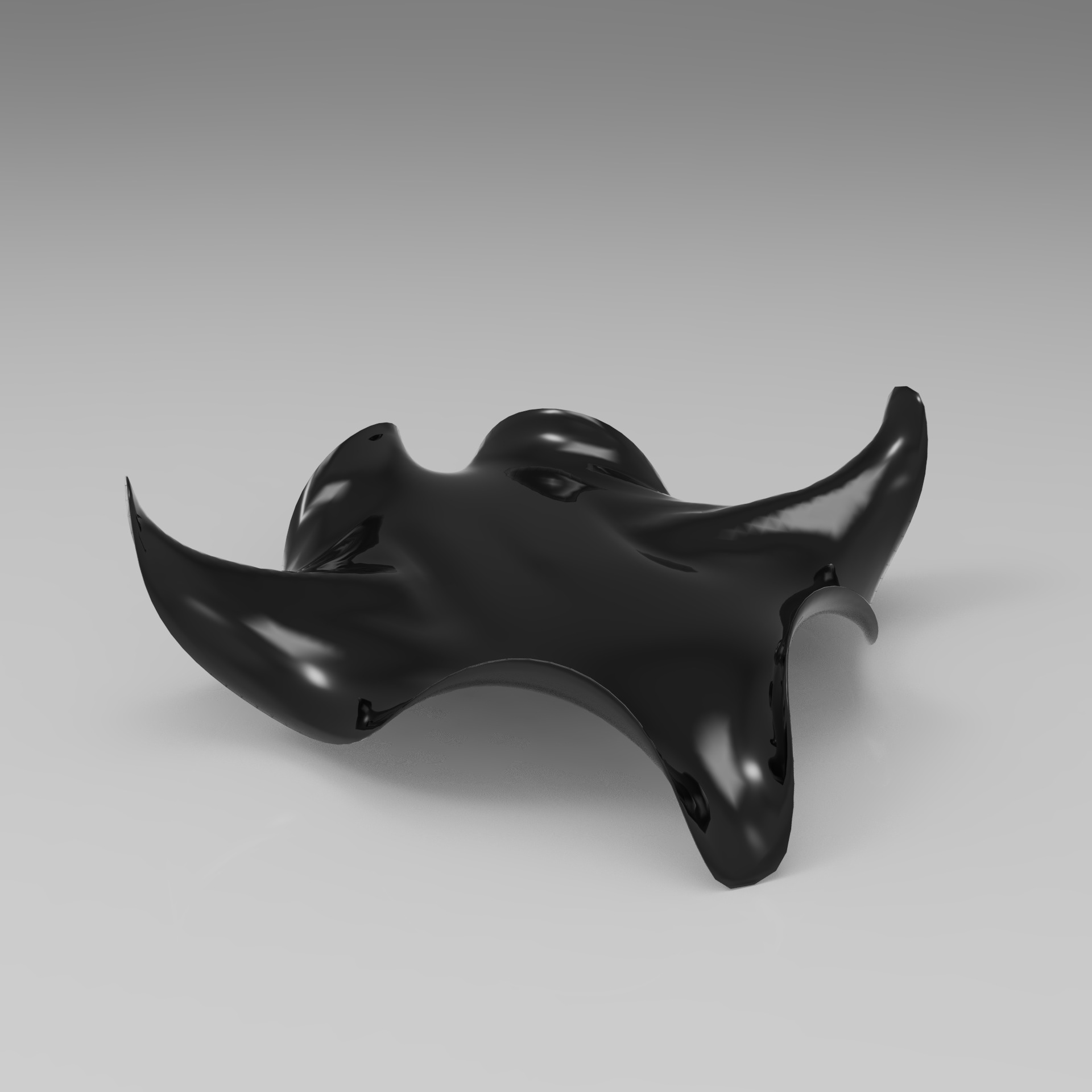
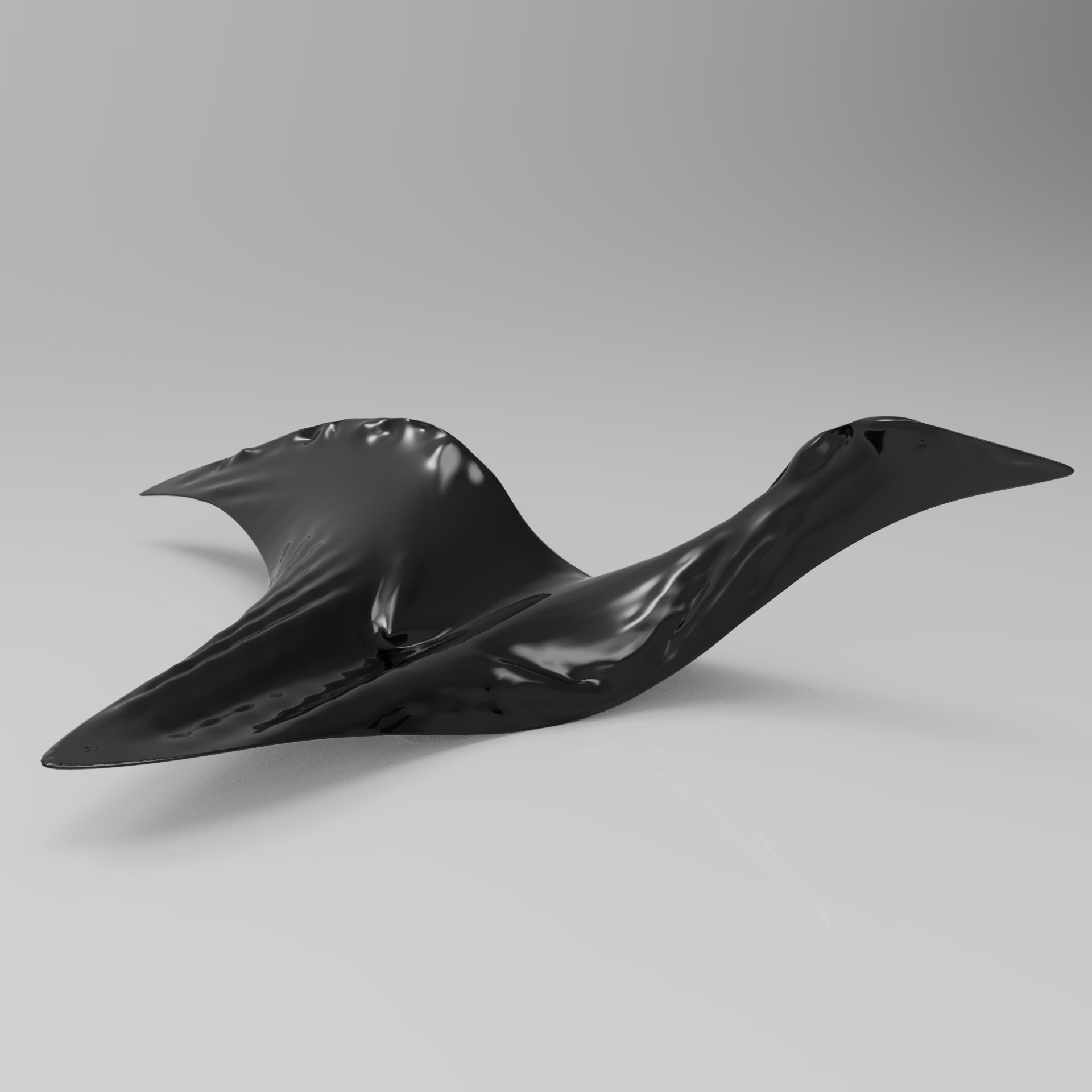
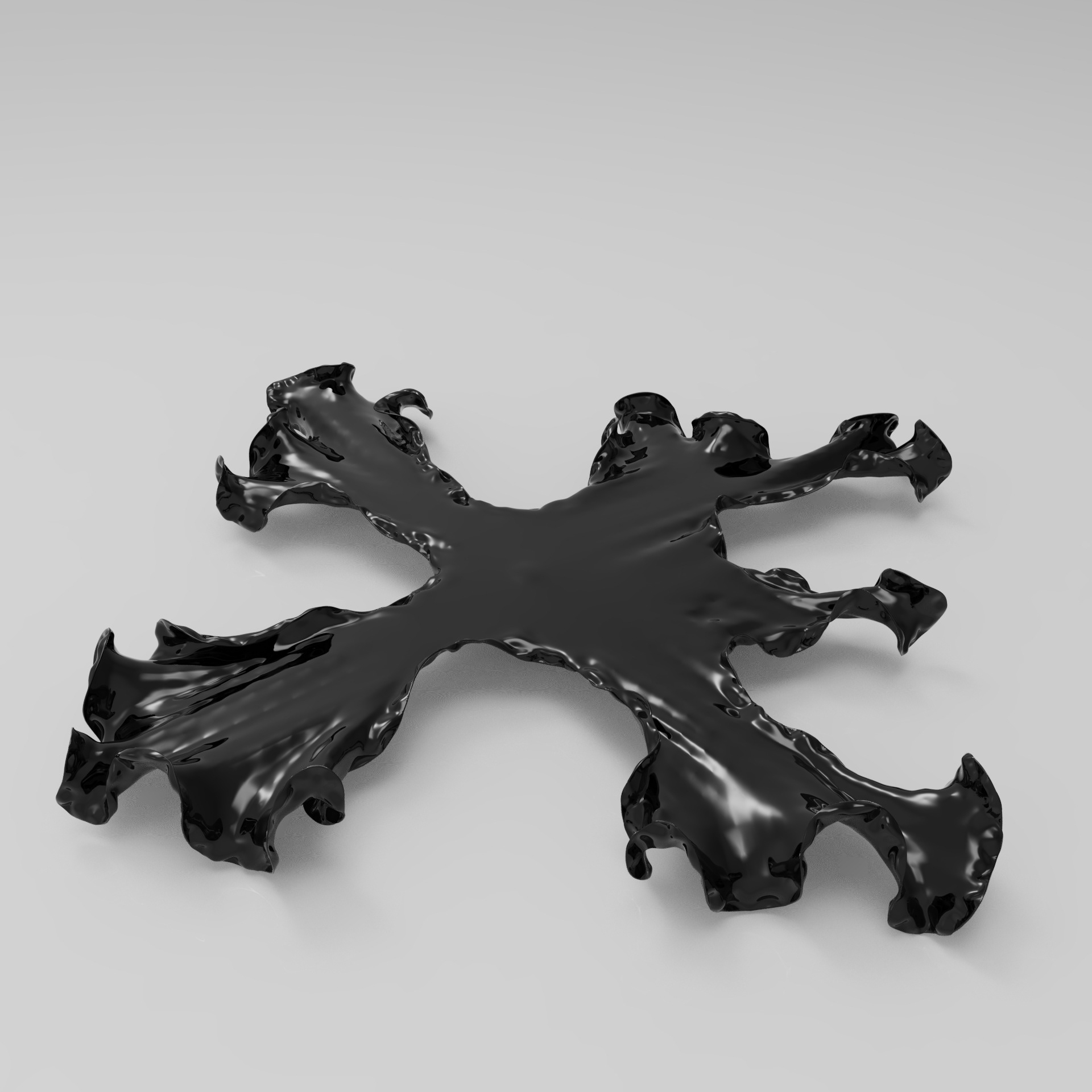
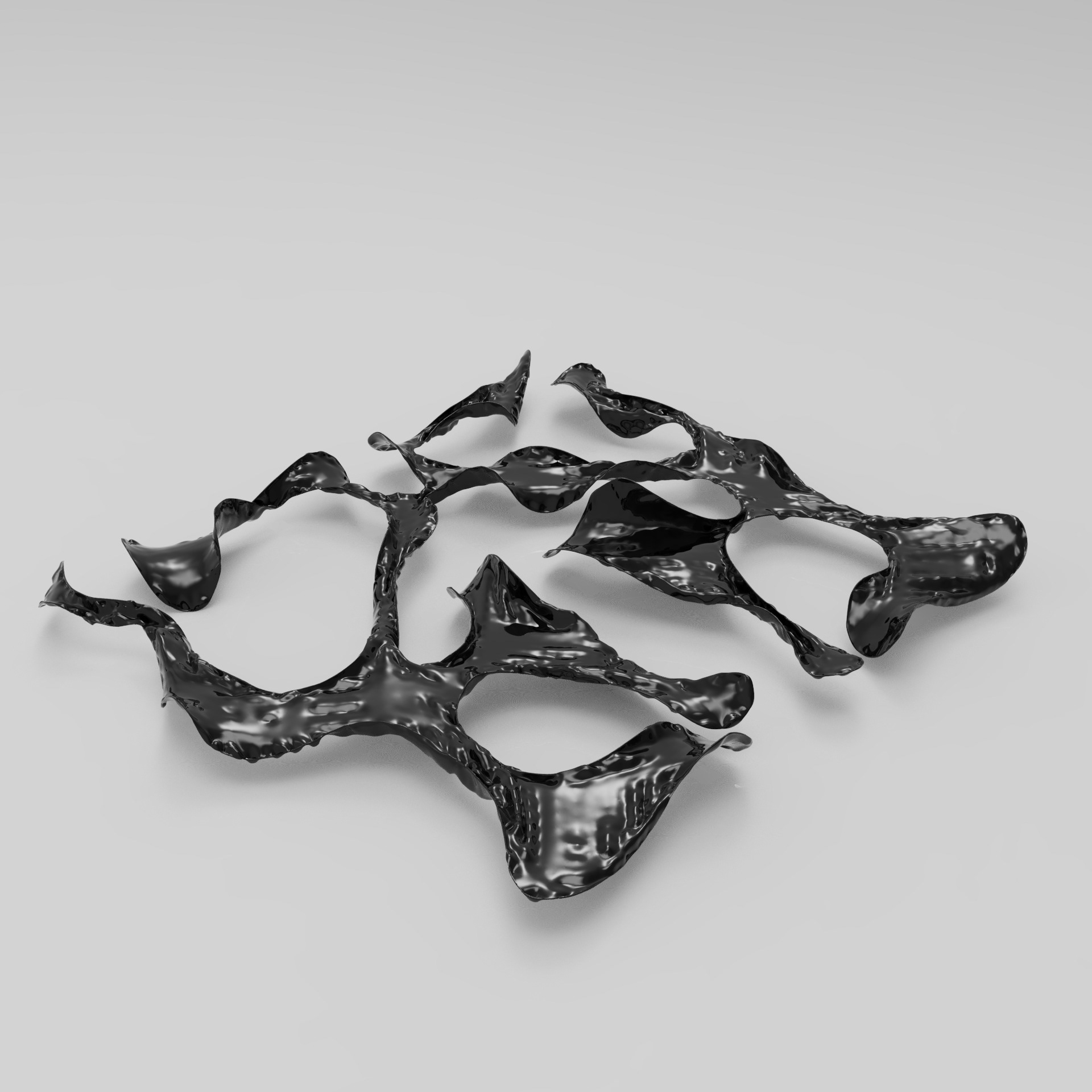
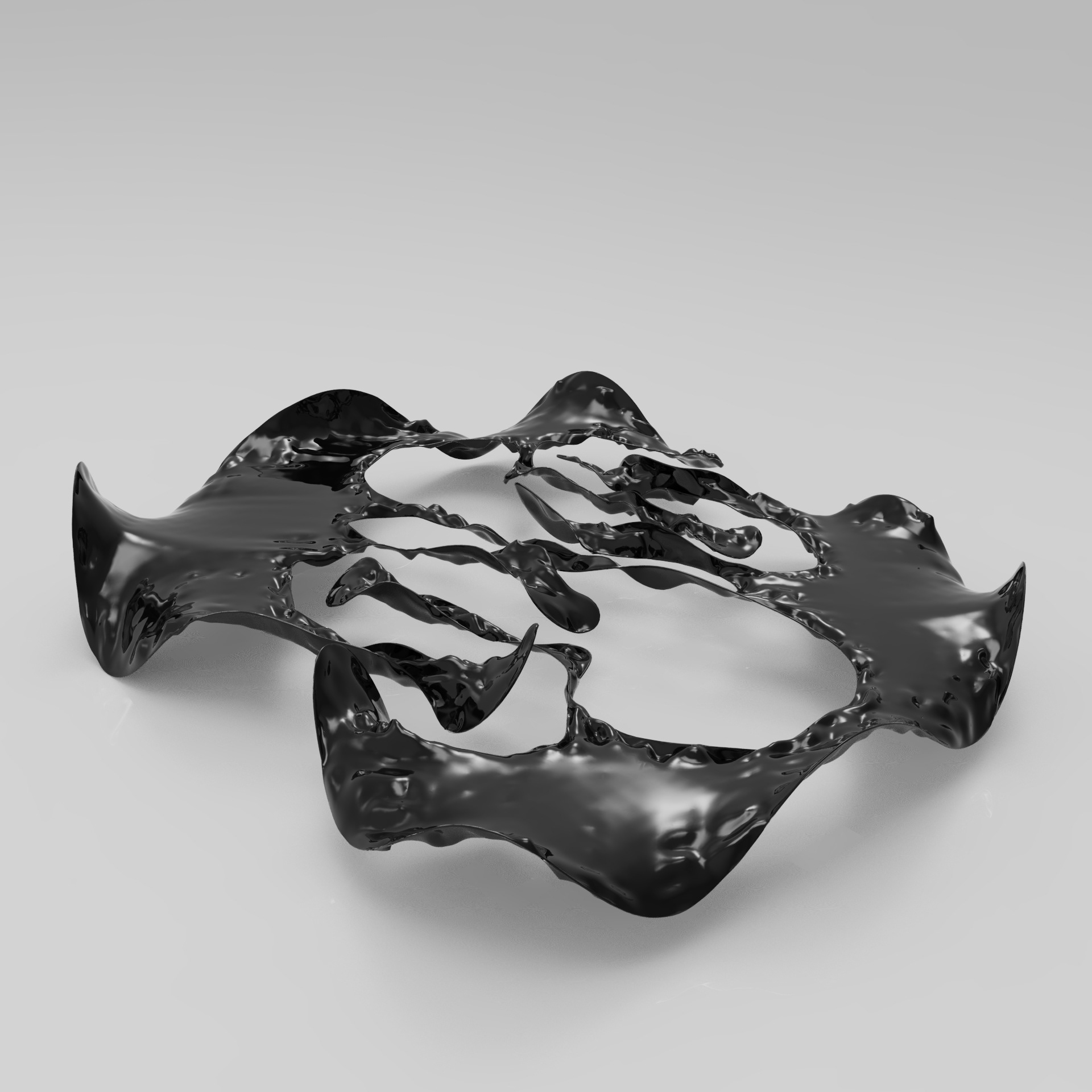
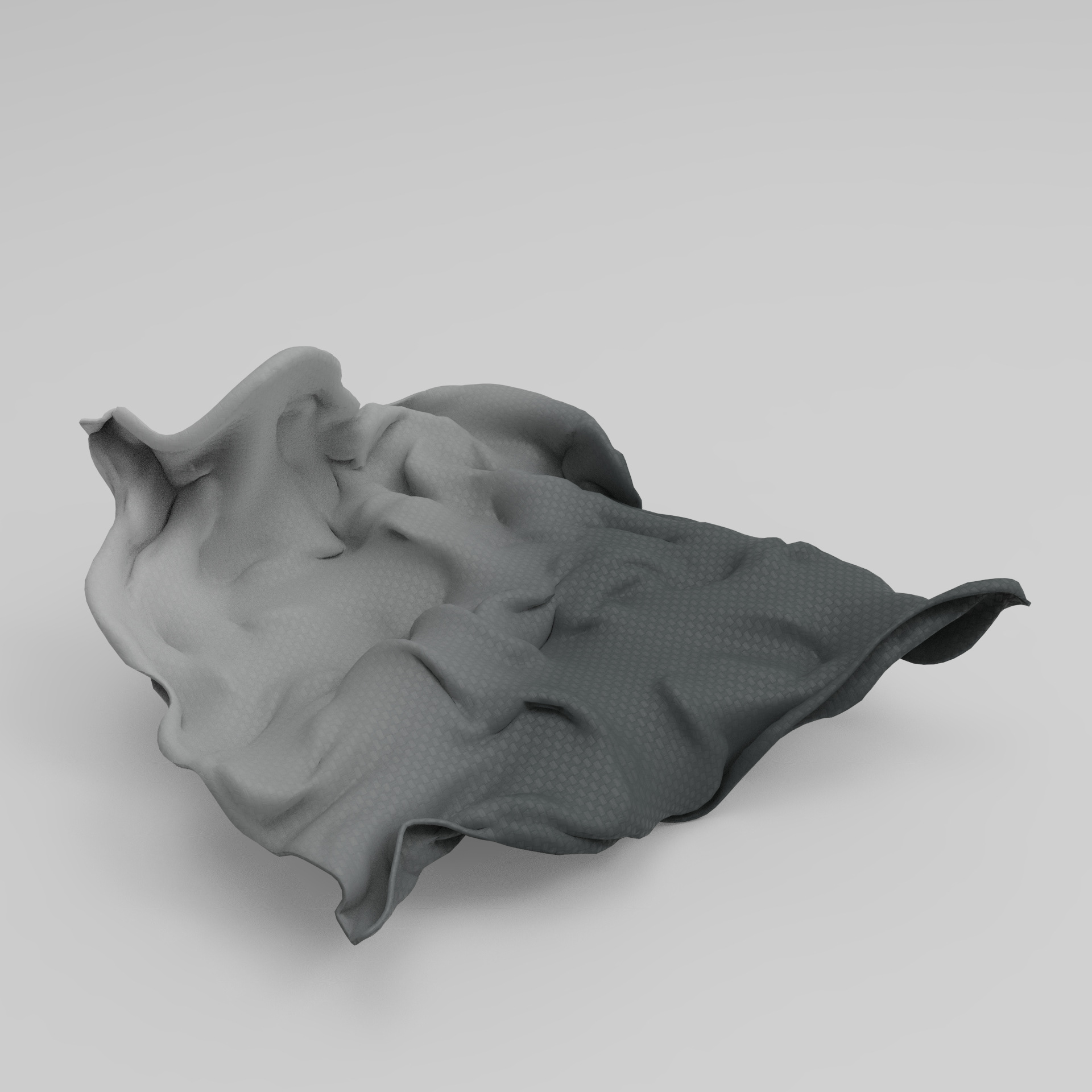
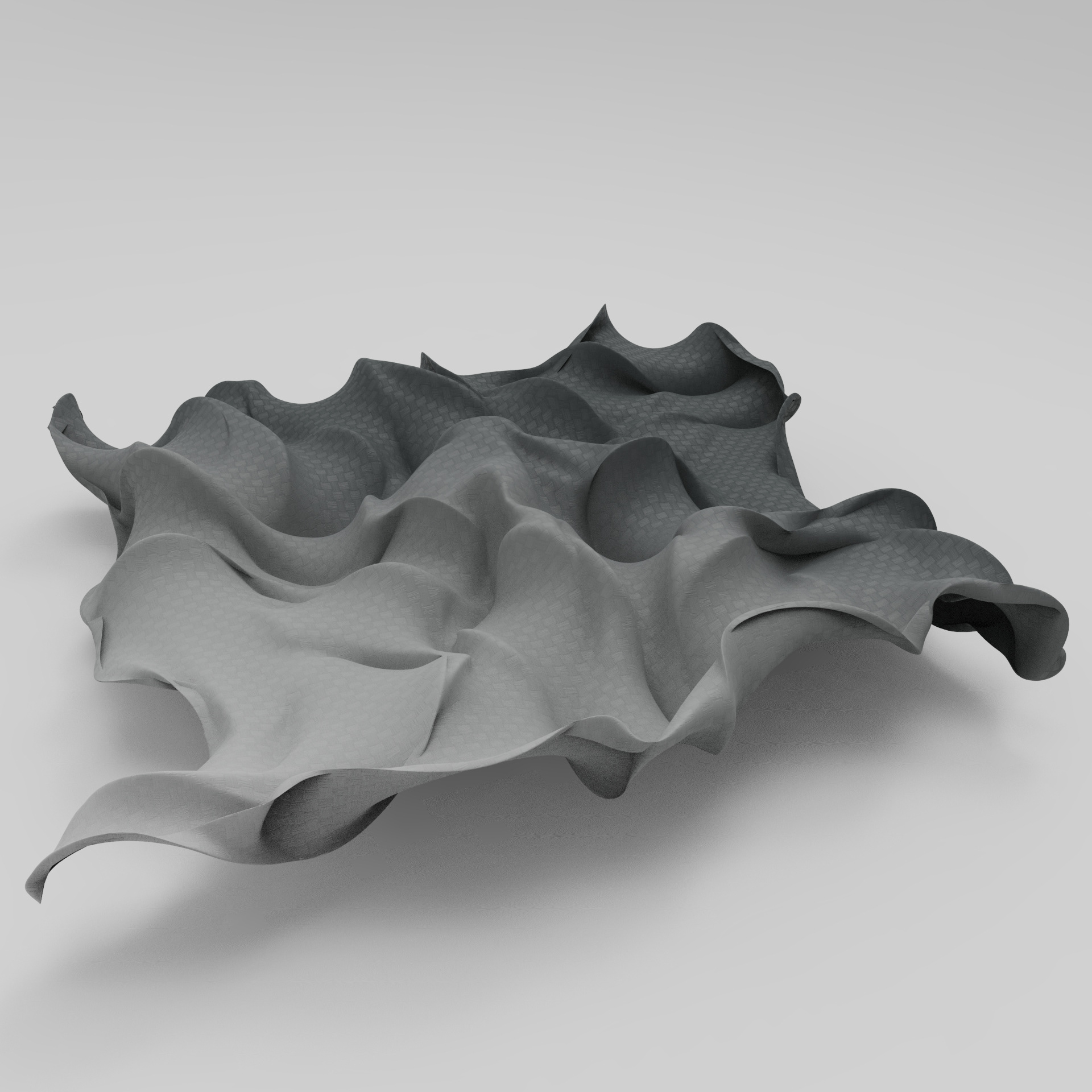
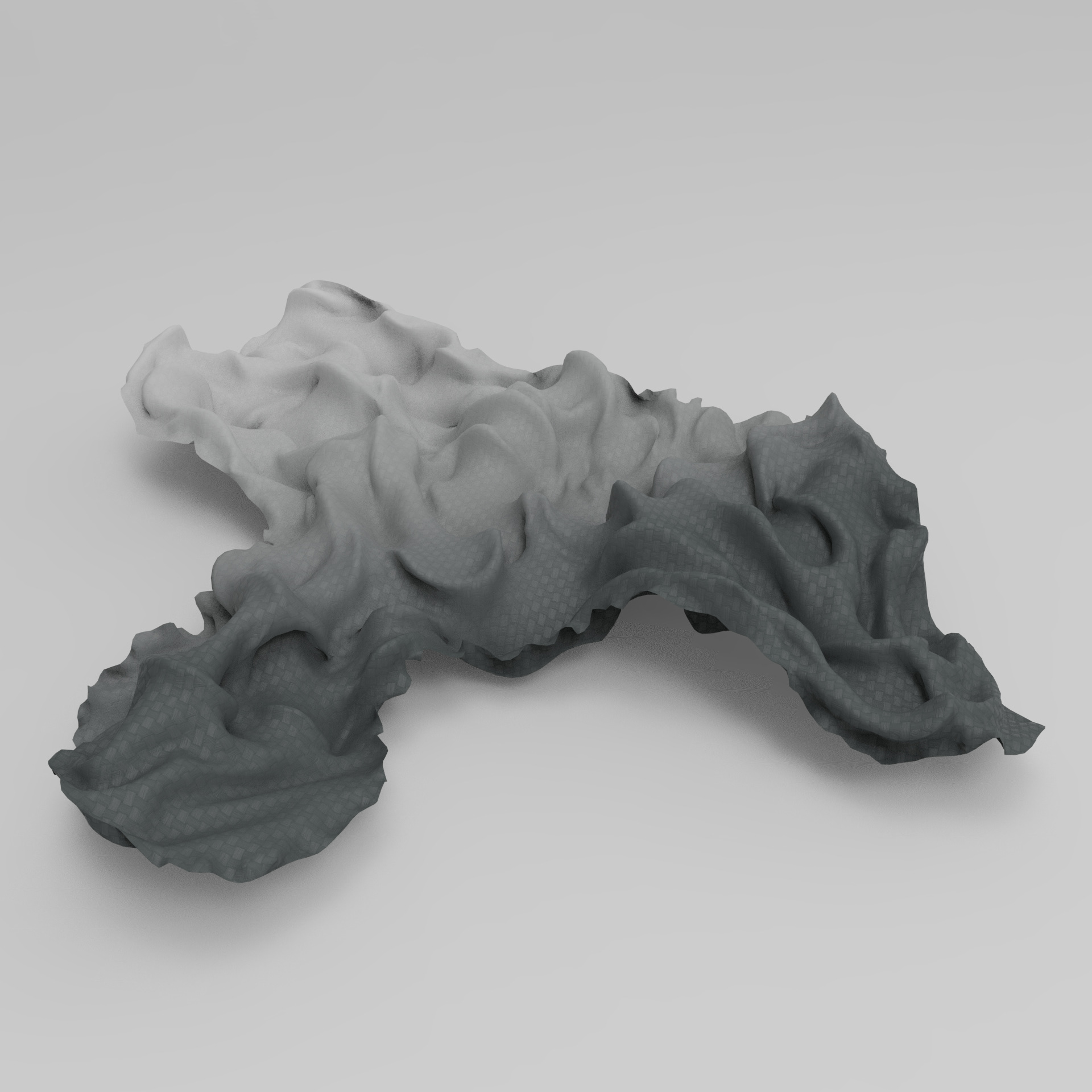
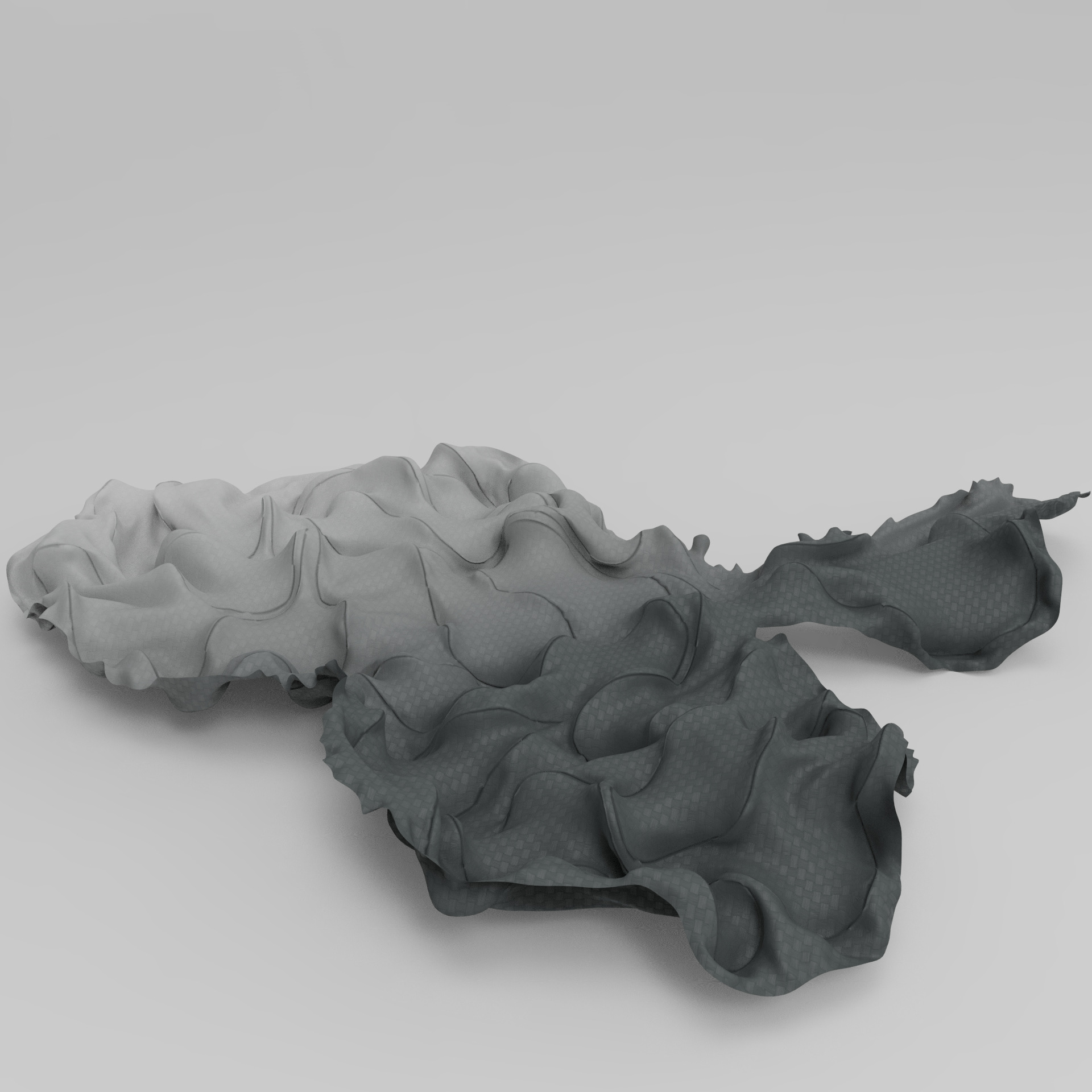
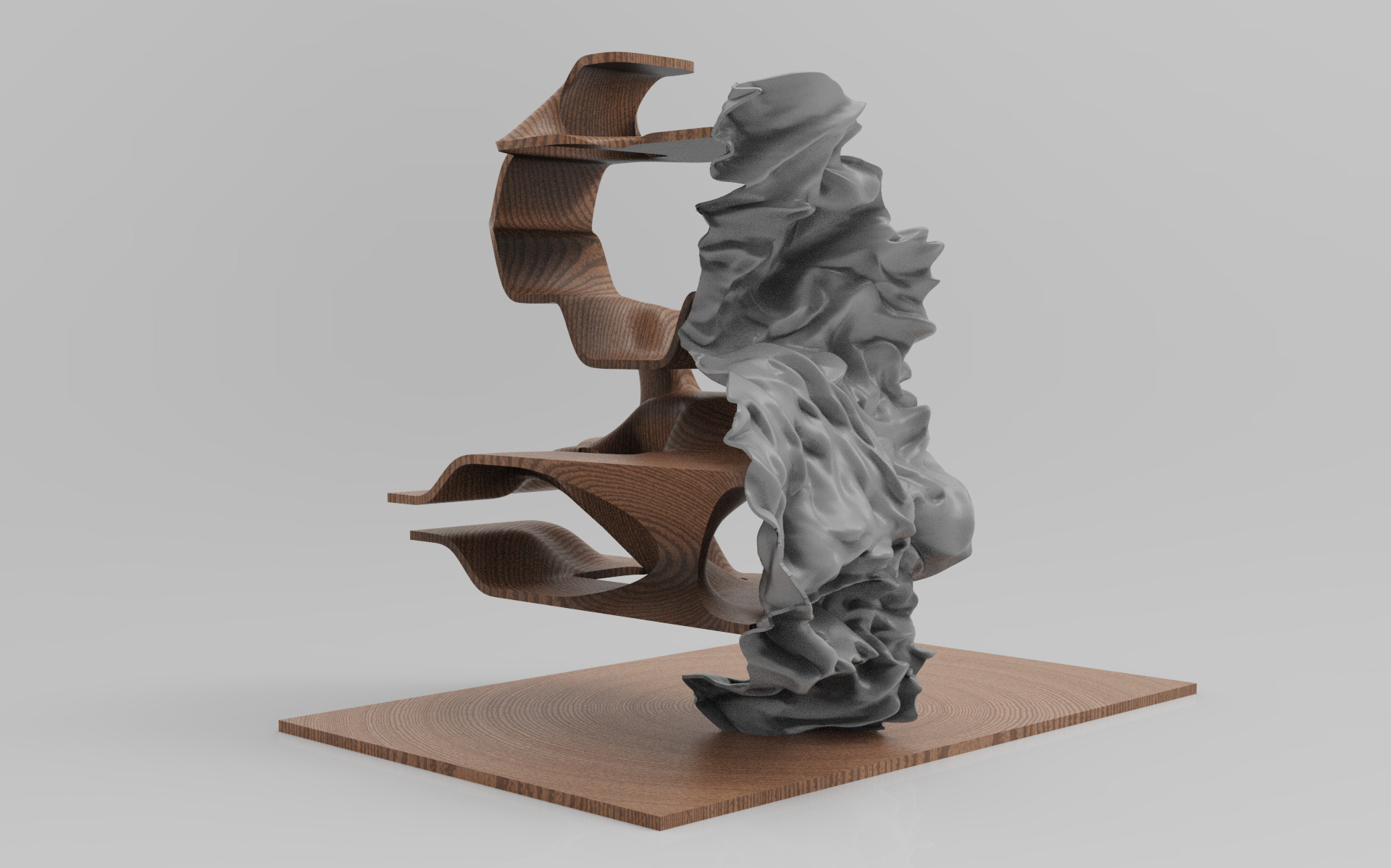
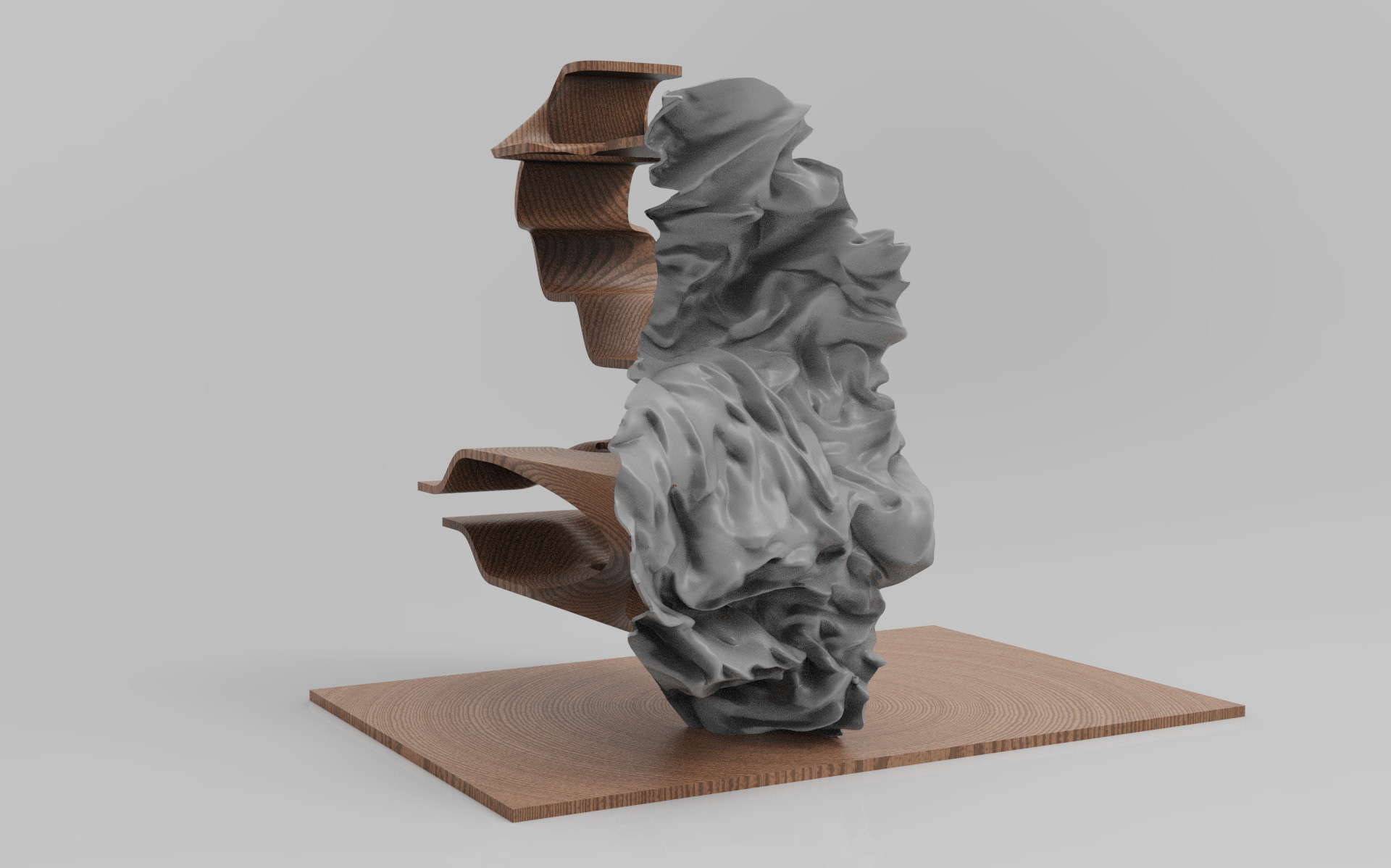